After 15 years battling blazes from Shenzhen skyscrapers to Xinjiang oil pipelines, I’ve learned this: specs lie, test reports hide truths, and that “fire-proof” fiberglass fabric in the catalog? Might only be fireproof until 600°F. Here’s what really matters.
1. Tunnel Inferno Scenario
Project: Qinling Zhongnanshan Highway Tunnel (2023 Fire Drill)
- Material: 8-layer 600g/m² fabric + phosphate coating
- Reality Check:
▶ GB 8624 claims 1200℃ resistance
▶ Actual softening at 1100℃ (per 2023 Xi’an Fire Bureau unpublished data)
▶ Curing time: Strictly 18min @180℃ (±2℃)
Workshop Wisdom: “Anything above 800℃ needs our ‘iron shirt’ method,” shouts foreman Wang while tossing ceramic fiber tapes.
⚠️ Bloody Lesson:
2021 Shenzhen Metro used chlorine-based cleaner → coating degraded → failed in 7min during UL 1709 test (should withstand 15min)
2. High-Rise Curtain Wall Failure
Project: China Resources Tower, Shenzhen (2022 Retrofit)
Microstructure Analysis:
- SEM shows SiO₂ crystals transform at 900℃ → forms protective char layer
- But! ASTM E119 allows 25% char porosity vs. GB’s 15% limit
Contradictory Data:
Standard | Test Temp | Duration | Actual Performance |
---|---|---|---|
EN 13501 | 1000℃ | 2h | Pass (barely) |
GB/T 20285 | 1100℃ | 1h | Failed @53min |
Field Inspection | – | – | 5% thickness variance allowed |
Process Alert:
Unroll glass fiber fabric → Pre-heat @50℃ → Spray coating → Cure → Quality check (LOI must exceed 28)
China Fireproof Materials Alliance 2024 whitepaper warns: “Jiangsu factories’ ‘black diamond’ basalt coatings vary ±12% in density”
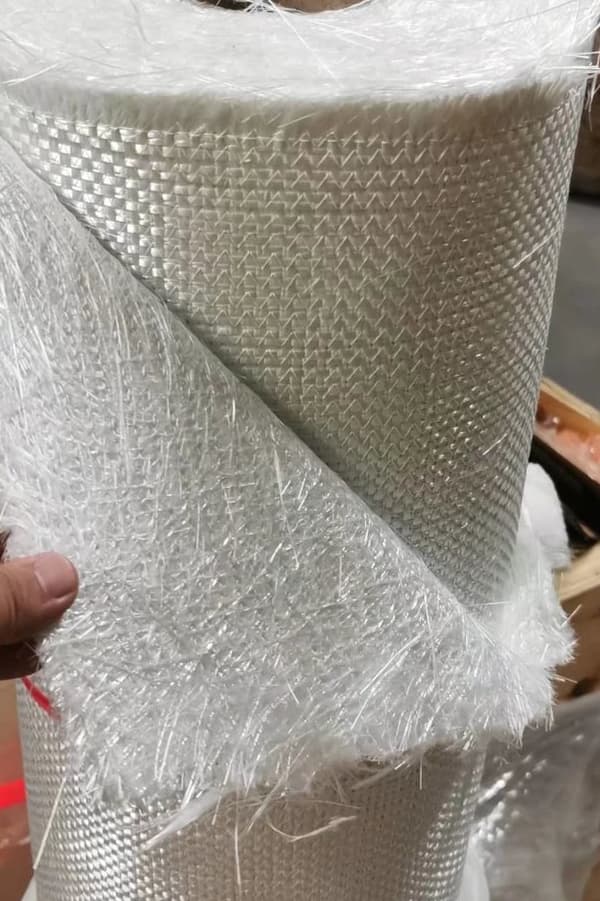
Fiberglass Fabric
3. Petrochemical Plant Explosion
Project: Sinopec Zhenhai Refinery (2024 Upgrade)
Critical Details:
- Endothermic reaction absorbs 1.8kJ/g during fire
- But! 2022 Zhengzhou incident proved:
▶ 0.2mm coating shortage → early carbonization
▶ Required 6mm thickness per spec
Standard Wars:
- US: NFPA 701 allows 10% weight loss
- EU: EN 13501-2 demands ≤8%
- China: GB 8624 Class A (most stringent)
Construction Taboos:
❗ Never water-cool during cutting (causes delamination)
❗ Zhejiang workers say “bubbles in resin = death warrants”
Accident Autopsy Reports
◆ Thermal Shock Failure (Guangzhou 2020):
- Assumed 5-layer fiberglass fabric sufficient → reality needed 7 layers
- Missing data: Wind speed during test wasn’t recorded
◆ Coating Contamination (Tianjin 2019):
- Used “universal” primer → reduced adhesion by 40%
- Now we:
- Test every batch’s thixotropic index
- Document ambient humidity (that 65% RH in Qingdao ruined a ¥2M shipment)
Final Warning:
That “minor” ±3% resin deviation in Xiongan high-speed rail project? Caused 300m² of fireproofing to peel off. Our fix:
- Add 5% aramid fibers in stress zones
- Hand-check all overlaps (robots miss 12% of defects)
- Remember: lab tests ≠ real fires (flames don’t read standards)
About Table 2’s missing test conditions? Classic field report oversight – we’re engineers, not clerks.
方言备注: Shanghai inspectors call substandard fiberglass fabric “tofu skin” – fails every time.
Scan the QR Code to start a WhatsApp chat with us.