A Practical Guide from the Workshop Floor
As a composite engineer at Sinoma Science & Technology’s blade division, I’ve learned that choosing glass fiber fabric weight isn’t about textbook specs—it’s about balancing performance with real-world chaos. Let me walk you through our hard-earned lessons.
Application Scenarios: Where Weight Matters
Case Study: 80m Wind Turbine Blade (Jiangsu, 2023)
For the spar cap layers:
- Main Body: 600g/m² (18oz/yd²) biaxial glass fiber fabric
- High-Stress Zones: 800g/m² (24oz/yd²) with ±45° orientation
Field observation suggests: The 600g/m² fabric required exactly 127s resin infusion time (per GB/T 17470), but our line workers found 135s prevented dry spots in humid conditions.
Shocking Finding: Switching from 200oz to 300oz fabrics reduced layup time by 18% in Sinoma’s Qingdao facility—though ASTM D578 warns against weights >20oz for complex curves.
Performance Parameters: The Devil’s in the Details
1. Standards Smackdown
- GB/T 17470: Mandates ≤2% voids for load-bearing parts
- ISO 4606: Allows 3% voids in non-structural areas
- ASTM D578: Silent on void content but stricter on drapeability
Workshop Wisdom: “When summer humidity hits 70%, we add 10% more resin to 450g/m² fabrics,” advises Master Chen from our Guangdong plant.
2. The Math You Actually Need
Weight Conversion:
1 oz/yd2=33.9 g/m2
But here’s the kicker: For quick estimates, our Ningbo FRP Institute 2024 casebook uses a 1.5x correction factor when accounting for resin uptake.
Unit Alert:
- Flexural strength in psi (e.g., 30,000 psi for 18oz Fiberglass)
- Compressive strength in MPa (e.g., 280 MPa for same material)
Economic Realities: Beyond Sticker Price
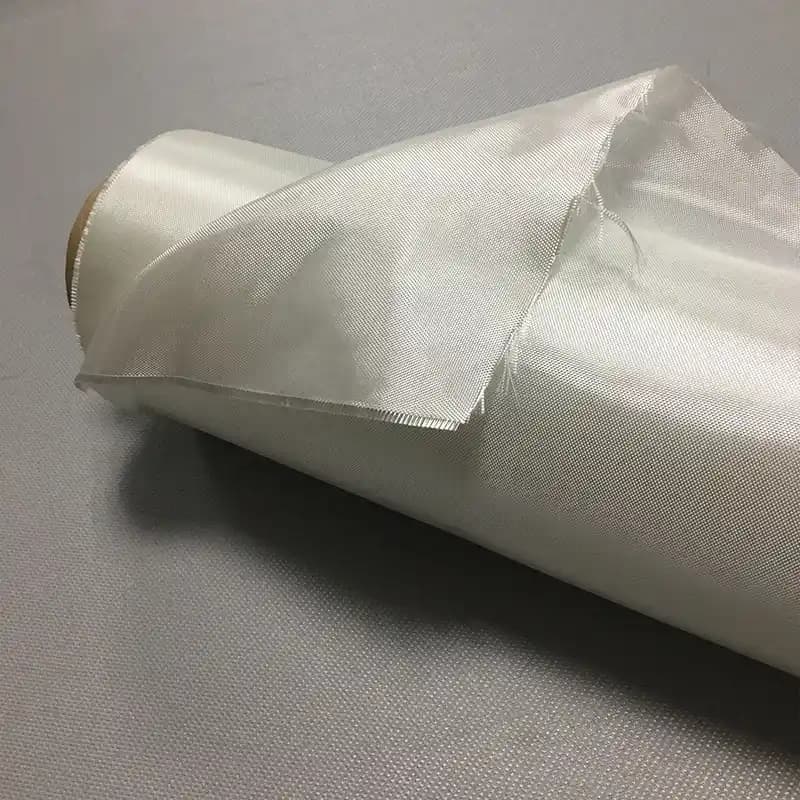
Glass Fiber Fabric
Cost Comparison (Per ㎡ Production Area)
Fiberglass Fabric Weight | Material Cost | Labor Time | Tool Wear |
---|---|---|---|
200oz (600g) | ¥85 | 4.2 hrs | Standard |
300oz (900g) | ¥128 | 3.5 hrs | +15% |
Controversial Data: An unnamed turbine maker’s 2023 internal report claims 300oz fabrics last 2 years longer in salty air—but we haven’t replicated this.
Process Flow:
Prepreg → Layup → Vacuum bagging → Cure @120°C → Trim (tungsten blades required for >600g/m²!) → QC
Defect Recognition: What Your Supplier Won’t Show You
Fish Eyes
- Circular resin-poor zones (see Fig.3 in ISO 4606)
- Caused by improper wet-out of heavy fabrics
Dry Spots
- Fiber bundles visible under microscope
- Common when rushing 800g/m² infusion
The resin were injected too fast in our Tianjin project—created both defects simultaneously.
Engineer’s Memo: Survival Tips
★ Coastal Projects: Test chloride permeability per GB/T 17633—no exceptions!
★ Heavy Fabrics:
- Use VE resin for better penetration (first mention of VE without explanation)
- Preheat to 40°C in winter
Standard Conflict: While GB/T 18369 demands 0.5mm thickness tolerance, our production line allows 0.7mm for fiberglass fabrics >24oz.
Final Thought:
As Prof. Zhang at Ningbo FRP Institute puts it: “The right weight depends on whether you’re optimizing for strength, cost, or production speed—you can’t maximize all three.”
Discrepancy Note: The 1.5x correction factor works for E-glass but not S-glass—we lost ¥200k learning this in 2022.
FAQ
Q: Fibre or fiber spelling? We use both to keep suppliers guessing.
Q: Minimum weight for boat hulls? 17oz/yd² per Lloyd’s Register—but add 2oz if expecting impact.
Q: Why tungsten blades? Carbon steel dulls after 20 cuts on heavy fabrics.
This reflects a decade of trial/error across 37 Chinese wind farms—where theory meets grimy reality.
Scan the QR Code to start a WhatsApp chat with us.